Since its origin, Rigo has always been at the forefront of techniques focusing on innovation and continuous improvement. The first major milestone was the investment in the development of the production process of paint rollers through Thermofusion, being to this day the way all rollers are manufactured at Rigo, regardless of the type of fabric.
Research & Development

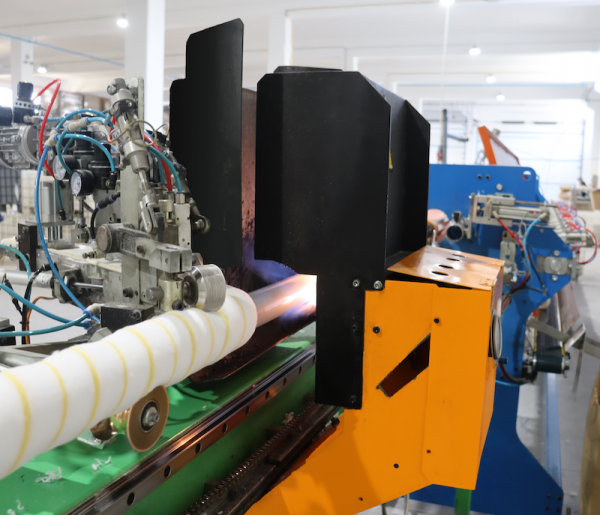

The thermofusion process dispenses the use of glues or resins between the fabric and the polypropylene tube.
For the assembly, the tube is heated at a high temperature in the vulcanizer, which allows the fabric base to be melted directly into the plastic, thus ensuring the durability of the product and its resistance to all kinds of solvents.
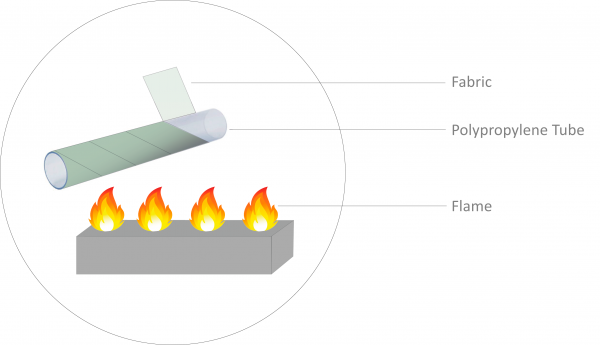

Another major innovation from Rigo was the start of ultrasonic welding of roller caps.
Ultrasonic welding is a process performed between two pieces of plastic where heat is generated by friction through mechanical oscillations. These oscillations activate the molecules causing them to move and the plastic to start melting. After a brief holding period under pressure, the two parts remain joined at the molecular level.
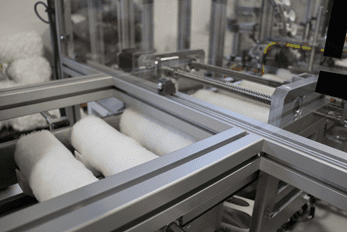

When it comes to paint brushes, there is also close collaboration with paint factory laboratories to develop the best formulas to achieve the most efficient bristles, adapted to the types of paint produced. For example, in the Junior and Minor brushes the bristles are composed of 30% natural and 70% synthetic bristles, with the natural bristles on the center of the brush head.
This formula allows for great efficiency in painting based on the relationship between absorption, retention, and the quality of the finish.
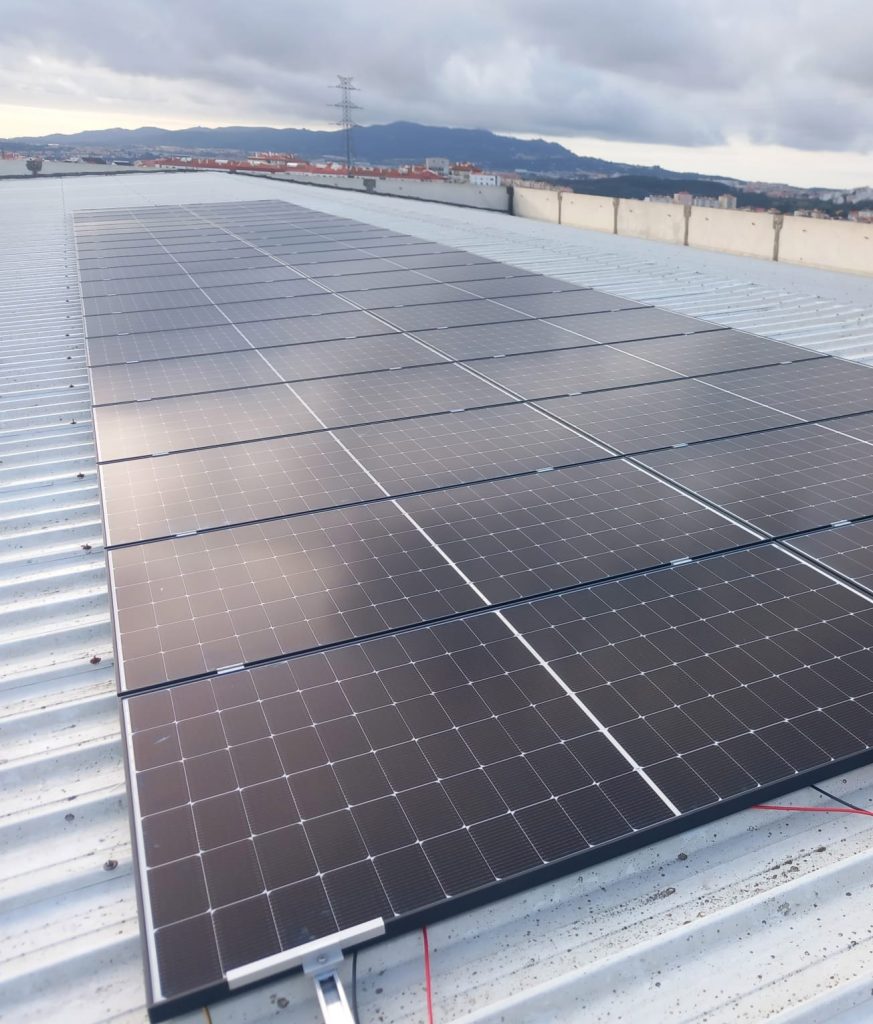

At Rigo, we are committed to continuous improvement, developing new formulas that combine quality, competitiveness and ecology. Faced with the imminent challenge of adopting sustainable solutions, we have created a new paint roller concept in Portugal: the CLIP Roller. The CLIP Roller allows the painter to maximize the use of the same frame for several loads, significantly reducing the waste of wire and plastic.
With more than 40 plastic molds and 80% of its production made from recycled plastic, Rigo’s products are highly ecological and competitively priced.
Also on our journey towards sustainability, we have invested in solar panels at the factory, reducing our carbon footprint and using clean, renewable energy. This initiative allows us to make production more efficient and environmentally friendly, contributing to a more sustainable future. Day by day, we are becoming greener.